Material Requirement Planning (MRP)
Material Requirement Planning (MRP) adalah suatu sistem, metode atau teknik perencanaan dan penjadwalan dalam memproyeksikan atau menentukan kebutuhan-kebutuhan (kuantitas dan waktu) suatu bahan, material atau persediaan berdasarkan urutan prioritas sesuai dengan jadwal induk produksi (Master Production Schedule).
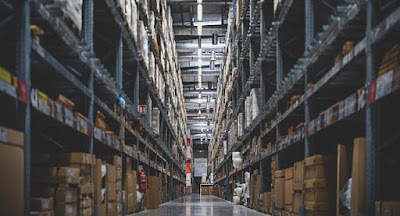
Material Requirement Planning (MRP) atau perencanaan kebutuhan material pertama kali dikenalkan oleh Joseph Orlicky dari J.I Case Company pada tahun 1960. MRP digunakan untuk menjamin dan mendukung kelancaran produksi, ketepatan waktu penerimaan bahan baku dan bahan pendukung lainnya oleh pihak produksi.
Material requirements planning (MRP) merupakan metode perencanaan (planning) dan penjadwalan (scheduling) pesanan dan inventori untuk item-item yang termasuk dalam dependent demand adalah bahan baku (raw material), bagian dari produk (parts), subperakitan (subassemblies), dan perakitan (assemblies).
MRP adalah suatu metode penjadwalan yang digunakan untuk merencanakan pembelian bahan baku dengan melihat ketersediaan kapasitas bahan baku agar keperluan produksi tidak terhambat. MRP adalah sistem yang mengatur jadwal untuk mengidentifikasikan bagian-bagian yang spesifik dan material yang diperlukan untuk memproduksi produk akhir, jumlah yang pasti diperlukan dan tanggal kapan pesanan untuk material-material ini harus dikeluarkan dan diterima atau diselesaikan dalam siklus produksi.
Pengertian MRP
Berikut definisi atau pengertian dari Material Requirement Planning (MRP) atau perencanaan kebutuhan bahan dari beberapa sumber buku dan referensi:
- Menurut Rangkuti (2004), MRP adalah suatu sistem perencanaan dan penjadwalan kebutuhan material untuk produksi yang memerlukan tahapan/proses.
- Menurut Nasution dan Prasetyawan (2008), MRP adalah suatu metode untuk memproyeksikan kebutuhan-kebutuhan akan komponen individual dari suatu produk. Sistem MRP mempunyai tiga fungsi utama, yaitu kontrol tingkat persediaan, penugasan komponen berdasar urutan prioritas, dan penentuan kebutuhan kapasitas (capacity requirement).
- Menurut Kumar dan Suresh (2008), MRP adalah teknik untuk menentukan kuantitas dan waktu untuk pembelian item permintaan dependen yang diperlukan untuk memenuhi kebutuhan jadwal induk produksi (Master Production Schedule).
- Menurut Heizer dan Render (2005), MRP adalah sebuah teknik permintaan terikat yang menggunakan daftar kebutuhan bahan, persediaan, penerimaan yang diperkirakan, dan jadwal induk produksi untuk menentukan kebutuhan material.
Tujuan MRP
Material Requirement Planning (MRP) bertujuan untuk mengendalikan tingkat persediaan kebutuhan bahan baku, item yang perlu diprioritaskan, dan waktu yang tepat dalam menyediakan bahan baku. Adanya MRP dapat memberikan informasi yang tepat terkait proses produksi hingga barang jadi diterima pelanggan. Selain itu, MRP membuat setiap unit kerja dapat berjalan dengan baik sehingga dapat meningkatkan efisiensi selama proses produksi di perusahaan.
MRP mengatur perencanaan yang harus dilakukan oleh perusahaan dalam melakukan pengelolaan bahan baku agar pemesanan bahan baku tidak berlebihan maupun kekurangan. Pendekatan MRP berkaitan dengan perhitungan kebutuhan bahan baku dalam sebuah periode perencanaan yang berurutan. Menurut Herjanto (2004), tujuan dari Material Requirement Planning (MRP) adalah sebagai berikut:
a. Meminimalkan persediaan
MRP menentukan berapa banyak dan kapan suatu komponen diperlukan disesuaikan dengan jadwal induk produksi (Master Production Schedule). Dengan menggunakan metode ini, pengadaan (pembelian) atas komponen-komponen yang diperlukan saja sehingga dapat meminimalkan biaya persediaan.
b. Mengurangi risiko karena keterlambatan produksi atau pengiriman
MRP mengidentifikasi banyaknya bahan dan komponen yang diperlukan baik dari segi jumlah dan waktunya dengan memperhatikan waktu tenggang produksi maupun pengadaan komponen, sehingga dapat memperkecil risiko tidak tersedianya bahan yang akan diproses yang dapat mengakibatkan terganggunya rencana produksi.
c. Komitmen yang realistis
Dengan MRP, jadwal produksi diharapkan dapat dipenuhi sesuai dengan rencana, sehingga komitmen terhadap pengiriman barang dapat dilakukan secara lebih realistis. Hal ini mendorong meningkatnya kepuasan dan kepercayaan konsumen.
d. Meningkatkan efisiensi
MRP juga mendorong peningkatan efisiensi karena jumlah persediaan, waktu produksi, dan waktu pengiriman barang dapat direncanakan lebih baik sesuai dengan jadwal induk produksi.
Persyaratan dan Asumsi MRP
Material Requirement Planning (MRP) bertujuan untuk menghasilkan informasi persediaan yang mampu digunakan untuk mendukung melakukan tindakan secara tepat dalam berproduksi. Agar MRP dapat berfungsi dengan efektif terdapat beberapa persyaratan dan asumsi yang harus dipenuhi. Menurut Heizer dan Render (2015), persyaratan Material Requirement Planning (MRP) yang digunakan sebagai dasar inputan informasi adalah sebagai berikut:
- Tersedianya Jadwal Induk Produksi (Master Production Schedule), yaitu suatu rencana produksi yang menetapkan jumlah serta waktu suatu produk akhir harus tersedia sesuai dengan jadwal yang harus diproduksi. Jadwal Induk Produksi ini biasanya diperoleh dari hasil peramalan kebutuhan melalui tahapan perhitungan perencanaan produksi yang baik, serta jadwal pemesanan produk dari pihak konsumen.
- Setiap item persediaan harus mempunyai identifikasi yang khusus. Hal ini disebabkan karena biasanya MRP bekerja secara komputerisasi dimana jumlah komponen yang harus ditangani sangat banyak, maka pengklasifikasian atas bahan, bagian atas bahan, bagian komponen, perakitan setengah jadi dan produk akhir haruslah terdapat perbedaan yang jelas antara satu dengan yang lainnya.
- Tersedianya struktur produk pada saat perencanaan. Dalam hal ini tidak diperlukan struktur produk yang memuat semua item yang terlibat dalam pembuatan suatu produk apabila itemnya sangat banyak dan proses pembuatannya sangat kompleks. Walaupun demikian, yang penting struktur produk harus mampu menggambarkan secara gamblang langkah-langkah suatu produk untuk dibuat, sejak dari bahan baku sampai menjadi produk jadi.
- Tersedianya catatan tentang persediaan untuk semua item yang menyatakan status persediaan sekarang dan yang akan datang (direncanakan).
Selain syarat di atas, terdapat beberapa asumsi yang diperlukan untuk menghasilkan suatu sistem pengoperasian MRP yang dapat berjalan secara efektif, yaitu sebagai berikut:
- Adanya suatu sistem data file yang saling berintegrasi serta ditunjang oleh adanya program komputer yang terpadu dengan melibatkan data status persediaan dan data tentang struktur produk. Data file ini perlu dijaga ketelitiannya, kelengkapannya serta selalu Up to Date sesuai dengan keperluan.
- Waktu ancang-ancang (lead time) untuk semua item diketahui, paling tidak dapat diperkirakan. Dalam hal ini waktu ancang-ancang dapat berupa interval waktu antara saat pemesanan dilakukan sampai saat barang tiba dan siap digunakan, tapi dapat pula berupa waktu proses pembuatan dari satu stasiun kerja untuk item atau komponen tersebut.
- Setiap komponen yang diperlukan dalam proses assembling haruslah berada dalam pengendalian. Dalam proses manufaktur ini berarti kita mampu memonitor setiap tahapan proses / perubahan yang dialami setiap item.
- Semua item untuk suatu perakitan dapat disediakan pada saat suatu pesanan untuk perakitan tersebut dilakukan. Sehingga penentuan jumlah, waktu kebutuhan kotor dari suatu perakitan dapat dilakukan.
- Setiap pengadaan pemakaian komponen bersifat diskrit. Misalnya bahan dibutuhkan 50 komponen, maka rencana kebutuhan bahan mampu membuat rencana agar dapat menyediakan 50 komponen tersebut dan dipakai tanpa kurang atau lebih.
- Perlu menetapkan bahwa proses pembuatan suatu item tidak tergantung terhadap proses pembuatan item yang laninya. Hal ini berarti dapat dimulai dan diakhiri tanpa tergantung pada proses yang lainnya.
Komponen-komponen MRP
Menurut Hendra (2009), Material Requirement Planning (MRP) terdiri dari beberapa komponen, yaitu sebagai berikut:
a. Master Production Schedules (MPS)
Jadwal induk produksi merupakan rencana rinci tentang jumlah barang yang akan diproduksi pada beberapa satuan waktu dalam horizon perencanaan. Jadwal induk produksi merupakan optimalisasi ongkos dengan memperhatikan kapasitas yang tersedia dan ramalan permintaan untuk mencapai rencana produksi yang akan meminimalisir total ongkos produksi dan persediaan.
b. Struktur Produk dan Bill of Materials (BOM)
Setiap item dan komponen produk harus memiliki identifikasi yang jelas dan unik sehingga berguna pada saat komputerisasi. Hal ini dilakukan dengan membuat struktur produk dan Bill of Material (BOM) tiap produk. Informasi ini penting dalam penentuan kebutuhan kotor dan kebutuhan bersih suatu komponen. Struktur produk ini dibagi menjadi beberapa level/tingkatan. Level 0 (nol) adalah tingkatan produk akhir. Level di bawahnya (Level 1) merupakan sub assembly yang jika dirakit akan menjadi produk akhir. Level di bawahnya lagi (Level 2) merupakan sub-sub assembly yang membentuk sub assembly jika dirakit.
c. Catatan Persediaan (Inventory Record Files)
Sistem MRP didasarkan atas keakuratan data status persediaan yang dimiliki sehingga keputusan untuk membuat atau memesan barang pada suatu saat dapat dilakukan dengan sebaik-baiknya. Untuk tingkat persediaan komponen dan material harus selalu diamati. Jika terjadi perbedaan antara tingkat persediaan aktual dengan data persediaan dalam sistem komputer maka data persediaan dalam sistem komputer harus segera dimutakhirkan. MRP tidak mungkin dijalankan tanpa adanya catatan persediaan yang akurat.
c. Waktu Tunggu (Lead Time)
Syarat terakhir agar MRP dapat diterapkan dengan baik adalah diketahuinya waktu tunggu pemesanan komponen. Waktu tunggu (lead time) ini diperlukan mengingat MRP memiliki dimensi fase waktu yang akan sangat berpengaruh terhadap pola persediaan komponen. Waktu ancang ialah waktu yang diperlukan mulai dari saat pesanan item dilakukan sampai dengan saat item tersebut diterima dan siap untuk digunakan, baik item produk yang harus dibuat sendiri maupun item produk yang dipesan dari luar perusahaan. Waktu ancang sangat dibutuhkan dalam sistem rencana kebutuhan bahan, terutama dalam hal perencanaan waktu. Waktu inilah yang mempengaruhi kapan rencana pemesanan akan dilakukan.
Adapun hasil atau output dari Material Requirement Planning (MRP) diperoleh dua komponen data, yaitu sebagai berikut:
a. Laporan Primer (Primary Report)
Laporan primer adalah hal utama atau laporan normal yang digunakan untuk persediaan dan kontrol produksi, yang termasuk laporan ini adalah:
- Planned order, rencana pemesanan untuk masa yang akan datang.
- Order realeas notice, pesanan yang dikeluarkan, yang menunjukkan kapan harus dilaksanakan perencanaan pemesanan (planned).
- Changes in due dates, perubahan pada rencana pemesanan, penjadwalan ulang (dikarenakan keadaan cuaca atau lalu lintas).
- Concellation or suspension, pembatalan pesanan terbuka dikarenakan adanya pembatalan dari jadwal induk (MPS).
- Inventory status date, data keadaan persediaan.
b. Laporan Sekunder (Secondary Report)
Laporan sekunder adalah laporan tambahan dimana MRP dapat memilih program-programnya:
- Planning report, laporan perencanaan digunakan untuk meramaikan dan menetapkan kebutuhan persediaan dimasa yang akan datang
- Performance report, laporan pengendalian yang menentukan waktu pelaksanaan yang digunakan untuk mengevakuasi sistem operasi antara lamanya waktu menunggu komponen bahan baku dengan jumlah yang telah dipakai serta biayanya.
- Exception report, laporan penolakan memberikan informasi tentang adanya kesalahan keterlambatan pesanan, bahkan sisa dan komponen yang tidak ada, serta pengecualian untuk syarat-syarat pembelian.
Proses dan Tahapan MRP
Menurut Nasution dan Prasetyawan (2008), terdapat empat proses utama dalam pelaksanaan Material Requirement Planning (MRP), yaitu sebagai berikut:
a. Netting (Kebutuhan Bersih)
Netting atau kebutuhan bersih adalah suatu proses perhitungan untuk menetapkan jumlah kebutuhan bersih, yang besarnya merupakan selisih antara kebutuhan kotor dengan keadaan (yang ada dalam persediaan dan yang sedang dipesan).
b. Lotting (Kuantitas Pesanan)
Proses lotting adalah suatu proses untuk menentukan besarnya pesanan individu yang optimal berdasarkan pada hasil perhitungan kebutuhan bersih. Terdapat banyak alternatif untuk menghitung ukuran lot. Beberapa teknik diarahkan untuk ongkos set-up dan ongkos simpanan, ada juga yang bersifat sederhana dengan menggunakan jumlah pemesanan tetap atau dengan periode pemesanan tetap.
c. Offsetting (Rencana Pemesanan)
Langkah ini bertujuan untuk menentukan saat yang tepat untuk melakukan rencana pemesanan dalam rangka memenuhi kebutuhan bersih. Rencana pemesanan diperoleh dengan cara mengurangkan saat awal tersedianya ukuran lot yang diinginkan dengan besarnya lead time.
d. Explosion
Explosion merupakan proses perhitungan kebutuhan kotor untuk tingkat item atau komponen yang lebih bawah, tentu saja didasarkan atas rencana pemesanan. Dalam proses exploison ini data mengenai dua struktur produk sangat memegang peranan karena atas dasar struktur produk inilah proses exploison akan berjalan dan dapat menentukan ke arah komponen mana harus dilakukan.
Adapun menurut Herjanto (2010), tahapan atau langkah-langkah dalam proses Material Requirement Planning (MRP) adalah sebagai berikut:
- Melakukan analisis rencana produksi produk akhir (level 0), dimulai dari penetapan kebutuhan kasar (GR) yang jumlahnya sesuai dengan rencana produksi yang terdapat dalam MPS.
- Netting, yaitu menghitung kebutuhan bersih dari kebutuhan kasar dengan memperhitungkan jumlah barang yang akan diterima, jumlah persediaan yang tersedia dan jumlah persediaan yang telah dialokasikan.
- Menempatkan suatu pelepasan pemesanan (PO) pada waktu yang tepat dengan cara menghitung mundur (backward scheduling) dari waktu yang dikehendaki dengan memperhitungkan waktu tenggang perakitan/pembuatan produk akhir tersebut.
- Menjabarkan rencana produksi produk akhir ke kebutuhan kasar untuk komponen-komponennya (level 1) dengan memperhatikan kebutuhan per unit sesuai dengan daftar material (BOM). Untuk komponen level 1, kebutuhan kasar mengacu pada rencana pelepasan pesanan (PO) dari level 0.
- Proses analisis diteruskan ke komponen-komponen level berikutnya sampai semua komponen telah dianalisis.
- Dibuatkan rangkuman yang menunjukkan skedul pembelian komponen dasar (yang tidak dibuat/dirakit oleh perusahaan) dan skedul produksi jangka pendek per jenis item. Jadwal pembelian disampaikan kebagian pengadaan, sedangkan skedul produksi disampaikan ke lini-lini produksi terkait.
Daftar Pustaka
- Rangkuti, Freddy. 2004. Manajemen Persediaan Aplikasi di Bidang Bisnis. Jakarta: Raja Grafindo Persada.
- Kumar, S. Anil, dan Suresh, N. 2009. Operation Management. New Delhi: New Age International Publisher.
- Heizer, J., dan Render, B. 2005. Operations Management. Jakarta: Salemba Empat.
- Hendra, Kusuma. 2009. Manajemen Produksi: Perencanaan dan Pengendalian Produksi. Yogyakarta: Penerbit Andi.
- Nasution, A.H., dan Prasetyawan, Y. 2008. Perencanaan & Pengendalaian Produksi. Yogyakarta: Graha Ilmu.
- Herjanto, Eddy. 2010. Manajemen Operasi. Jakarta: Grasindo.